התיב"מ המכאני, לאן?
במשך כל שנות עיסוקי בתחום התיב"מ (תכנון ויצור בעזרת מחשב) ובעיקר בענף העיבוד השבבי עולה השאלה: " התיב"מ המכאני, לאן? " מה הוא עתיד התיב"מ? מה עוד ניתן להשיג שעדין לא השגנו? היכן ניתן לחסוך וליעל את תהליך העיבוד השבבי? והאם לא הגענו לקצה גבול היכולת בפיתוח כלים טכנולוגיים בתחום זה?
על שאלות אלו ועוד רבות אנסה לענות בכתבה זו ואולי להעלות מחשבות ורעיונות לתיב"מ "הדור הבא".
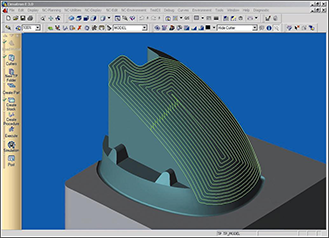
ההיסטוריה של התיב"מ המכאני הינה צעירה מאד בהשוואה להיסטוריה העתיקה של עיבוד המתכות שהיה הכרח המציאות ועצם קיומו של האדם הקדמון. בעוד האדם הקדמון צריך היה להשתמש באבנים או לחלופין באבזרי ריקוע שונים על מנת לעבד את ה"ברזל" שברשותו כדי ליצור כלי מלחמה שונים וכלי אוכל הזקוקים למחייתו היום יומית.
הצורך בעיבוד שבבי מדויק החל עוד בתחילת המאה הקודמת בזמן התפתחות תעשיית הרכב התעופה. ההכרח ליצור יחסיות בין חלקים נעים חייב את היצרנים ליצרם בדיוק מרבי על מנת שהרעיון התכנוני יהפוך למוצר מוחשי ועובד.
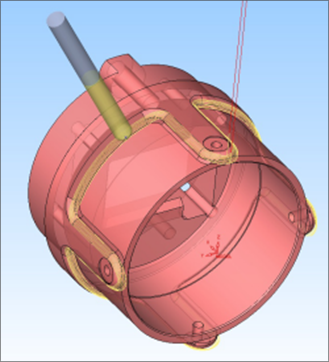
התכנון הראשוני בעבר היה בעזרת ניר, עיפרון וכמה נוסחאות מתמטיות לחישובי חוזק, אך מאחר והצורך ליצור "מכונות" מורכבות יותר, עמידות יותר, חכמות יותר ומעל לכל אמינות ובטיחותיות יותר, נזנח רעיון הניר והעיפרון ועברנו לדור המחשב. לא אפרט את ההיסטוריה בהתפתחות המחשב, אך כולנו היום מודים שאי אפשר בלי מחשב, המחשבים שולטים בכל אורח חיינו היומיומי.
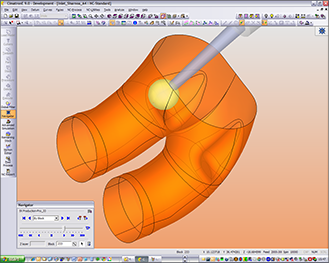
אנו בימינו כבר לא יודעים במה דברים עסקינן, אנחנו בעיבוד שבבי מגיעים לדיוק של אלפיות המילימטר ואף פוזלים לתחום הננומילימטר ואז מבקר האיכות במפעל "מעז" להגיד לנו "החלק פסול, יש חריגה של מיקרון מהטולרנס, יש להתחיל הכל מחדש".
כיום, ככל שתוכנת התכנון מתקדמת יותר כן גדל הצורך בתוכנת יצור חזקה יותר ובעלת יכולות טכנולוגיות גבוהות יותר. בכדי לאפשר את יצורו של החלק אשר תוכנן ע"י מהנדס אמביציוני שרואה לנגד עיניו, על מסך המחשב, איך הרעיון נהפך למוצר, (בדרך כלל ומבלי לפגוע בכבודם של המתכננים רובם לא יודעים מה זה ליצר בעיבוד שבבי את פרי עיצובם) ובכן, היצור בעיבוד שבבי לעיתים קרובות מסובך ביותר עד בלתי אפשרי.

כאן נחלצות לעזרתנו מכונות העיבוד השבבי ויצרני כלי החיתוך השונים. גם בתחום זה ישנה התפתחות עצומה וניתן להקדיש להתקדמות זו כמה כתבות נפרדות. לפי דעתי, ההתפתחות ביכולת העיבוד השבבי מהווה את השמן והזרז בהתפתחות התיב"מ המכאני.
חברת "סימטרון" שהינה חברה ישראלית בת למעלה מ 25 שנים, חרתה על דגלה את הצורך והיכולת להיות תמיד בראש חזית הטכנולוגיה ולצעוד במקביל עם התקדמות היכולות המכאניות של מכונות העיבוד השבבי וכלי החיתוך.
הרצון האולטימטיבי של כל בעל מפעל עיבוד שבבי הוא: שלא יעברו יותר מחמש דקות מרגע קבלת אישור ליצור החלק, החלק כבר יהיה ארוז ומוכן למשלוח לאחר שעבר את כל התהליך הארוך של תכנות ה- NC, יצור, תהליכים כימים וביקורת סופית על-מנת שיוכל להוציא חשבונית ללקוח ולהזדרז לגבות את התשלום.
אך מה לעשות שבין הרצוי למצוי הפער עדיין רב. חברת "סימטרון" מנסה לגשר על פער זה בזכות היכולת לקצר את זמן תכנות ה NC (הזמן העובר מאישור החלק ליצור ועד תחילת יצור החלק במכונת העיבוד השבבי) וכן קיצור זמן העיבוד של החלק במכונה.
High Speed Cutting
הטכנולוגיה המתקדמת ביותר כיום במכונות ה- CNC הינה H.S.C (High Speed Cutting) עיבוד שבבי מהיר, היכולת של המכונה "לרוץ" במהירות גבוהה, תוך כדי שמירה על מהירות אחידה בין העובד לכלי ללא עצירות או האטות, קירור נכון של הכלי תוך כדי פיזור השבבים, ומחשב "חכם" המסוגל לקרוא כמות גדולה של שורות Gcode במהירות תוך הסתכלות קדימה על המשך התוכנית על מנת לשמור על תנועה רציפה, ללא עצירות ובמהירות חיתוך נכונה ע"פ הגדרת יצרן הכלים בכדי לקבל טיב שטח טוב.
בתוכנת "סימטרון" לכרסום קימות כמה שיטות לנצל את יכולת ה- H.S.C של המכונה:
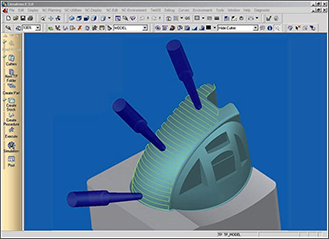
שימוש משכיל באופטימיזר כך שבכל שלב מהזמן שהכלי בחומר יפעל עליו עומס אחיד. הכיצד? התוכנה בכל שלב של העיבוד יודעת את כמות החומר הגלם הנשאר בעובד לאחר הפעולה האחרונה ואת נפח חומר הגלם על הכלי במגע כלי-עובד. המפעיל מגדיר את נתוני העיבוד הרצוי (בהתאם להגדרת היצרן) אשר משמש כסמן יחסי בין נפח השבב למהירות הקידמה. בהתאם לכך התוכנה תחשב בכל רגע נתון את מהירות העיבוד החדשה על-פי כמות חומר הגלם המוסרת ע"י הכלי, ז"א אם הכלי עמוס מדי (100% מקוטר הכלי) התוכנה תאט את מהירות הקידמה, אם הכלי עמוס חלקית באחוזים התוכנה תגביר את מהירות הקידמה. אופציה זו מאפשרת למפעיל המכונה לעבוד כל הזמן בניצול מקסימאלי של יכולות הכלי והמכונה וכתוצאה מכך קיצור זמני עיבוד משמעותיים.
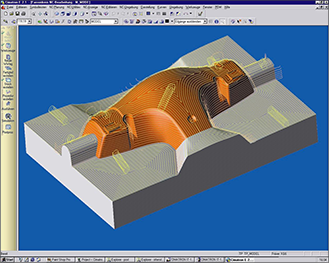
אפשרות שנייה: בלי לשנות את קידמת המכונה, כאשר התוכנה מזהה עומס שבב גדול על הכלי היא משנה את תנועת הכלי לתנועה טרכואידאלית – התקדמות ליניארית תוך תנועה ספיראלית של הכלי במישור XY ועל ידי כך מאפשרת למפעיל לשמור על קידמה מקסימאלית מבלי לדאוג לשבירת כלי עקב עומס רב. האפשרות של עבודה במהירות גבוהה ועומס שבב קטן על הכלי מאריכה את חיי הכלי, מעלה את ניצולת המכונה ומקצרת זמני עיבוד.
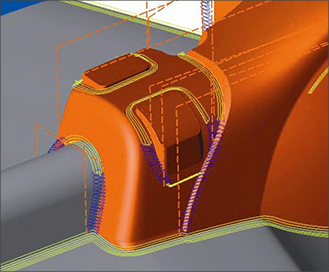
אופציה נוספת ואולי החשובה מכולן, היא ביטול התנועות החדות בשינויי כיווני עיבוד במכונה. לדוגמא: מעבר מתנועה לאורך ציר X לתנועה לאורך ציר Y מחייב את המכונה בתאוטה לאורך ציר X , עצירה רגעית בנקודה הסיבוב והאצה מחדש למהירות קידמה לאורך ציר Y. מתברר ששינוי מהירויות אלו ההאטה והתאוצה הם אחד הגורמים המשמעותיים בהגדלת זמן עיבוד חלק. "סימטרון", ע"י ביטול התנועות החדות וביצוע העגלה לכל הפינות, כמובן, תוך כדי התחשבות בזוית השינוי, מאפשרת למכונה לעבוד במהירות אחידה ביחס כלי-עובד, לחסוך זמן עיבוד ובהשגת טיב פני שטח טובים יותר מאשר בעיבוד הרגיל.
עיבוד בחמישה צירים
טכנולוגיה נוספת אשר בשנים האחרונות נכנסת יותר ויותר למפעלי העיבוד השבבי "הקטנים" (3-6 מכונות CNC ), היא עיבוד שבבי ממוחשב במכונות כרסום חמישה צירים. תרמו לכך הוזלת מחירי מכונות אלו יחסית לשנים עברו ויכולות התיב"ם החזקות המאפשרות תכנות מהיר ומדויק במרחב החמישה צירים.
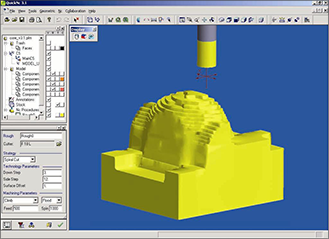
טכנולוגיה זו מאפשרת לסיים את העיבוד השבבי של החלק כמעט בדפינה אחת וכאשר מורידים את החלק מהמכונה נשאר רק צד אחד לעיבוד נוסף.
יכולת זו מאפשרת לקצר את זמן העיבוד של החלק, להגדיל את רמת הדיוק והיחסיות בין העיבודים השונים הנמצאים על מישורי העיבוד במרחב.
חבילת התוכנה של "סימטרון" מקנה יכולת עבודה בחמישה צירים מתמשכת (סימולטאנית), תוך כדי התחשבות במיקום העובד על השולחן (ישנה אפשרות למקם את העובד לא במרכז ציר הסיבוב והתוכנה תחשב אוטומטית את מיקומו המדויק ללא צורך להגדיר "בית" לכל זווית עיבוד), התחשבות באורך הכלי ביחס לספינדל וביחס לתפסנית (התוכנה תדאג להטות את הראש או השולחן של המכונה בכדי לשמור על מרחק ביטחון בינהם לבין העובד).
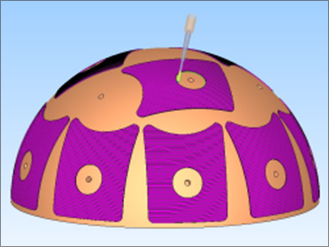
עבודה במכונה חמישה צירים מאפשרת "תפירה" של משטחים ברמת דיוק גבוהה, טיב פני שטח טובים יותר וזמן עיבוד קצר מאשר במכונות שלשה צירים. היכולת להטות את העובד בזוית רצויה באופן מתמשך מקנה שתי אפשרויות עיבוד:
עבודה על משטח עם כלי שטוח ופסיעות צידיות גדולות יחסית לעבודה עם כלי כדורי. תוכנת ה"סימטרון" דואגת לניצבות מקסימאלית בין תחתית הכלי לבין העובד. עבודה זו טובה בעיקר למשטחים קמורים.
עבודה על משטח עם כלי כדורי המחייב פסיעות צידיות קטנות, זאת אומרת, הרבה מהלכי מכונה על מנת לקבל את המשטח הרצוי. תוכנת ה"סימטרון" דואגת לעבוד עם הכלי בנקודת השקה ולהימנע בעבודה עם הפדחת שלו. מדוע? מכיוון שמהירות החיתוך במרכז הכלי היא אפס ועבודה עם תחתיתו של הכלי הכדורי תיתן טיב פני שטח גרועים. אי לכך יש חשיבות רבה לעבוד בנקודת השקה בצידו של הכלי הכדורי. יכולת השקה זו אפשרית אך ורך במכונות חמישה צירים ובעבודה סימולטאנית.
עיבוד שארית החומר
התקדמות טכנולוגיית הכרסום בשלושה צירים מושפעת באופן ישיר מהתפתחות המהירה של תוכנות התיב"מ. בעבר כדי לעבד משטח תלת ממדי ניזקק המפעיל למחשב ידני וע"י מציאת הנוסחה המתאימה וכתיבתה בשפת ה Gcode חושבו מהלכי המכונה. אמנם התוכנית הייתה קצרה מאד אך בכדי להגיע לנוסחה הנכונה בוזבז זמן רב ונדרש תכנת מקצוען. כל שינוי במשטח חייב חישוב מתמטי חדש וארוך.
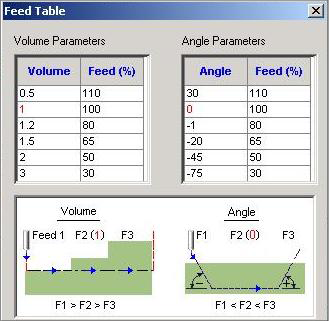
כיום כאשר המשטחים מתקבלים כמודל מתמטי ישירות מהמתכנן, תכנת ה CNC לא צריך לדעת מתמטיקה גבוהה. הוא פשוט נותן לתיב"מ לעשות את כל עבודת החישוב השחורה. ע"י כך הוא חוסך זמני חישוב (אשר בזמן זה המכונה היתה עומדת וממתינה לתכנת שיגמור להריץ את התוכנית) ומגדיל את היכולת בשינוי מידי של המוצר. אומנם התוכנית ארוכה מאד, אך למי אכפת כאשר בקר המכונה מסוגל לקלוט תוכנית ארוכה כמעט ללא הגבלה.
גם בתחום עיבוד זה התיב"מ "החכם" נתן את דגשיו. עבודה על חלק תלת ממדי כאשר קיימת חשיבות רבה לסדר הכלים העובדים. לא חוכמה לעבוד עם כלי אחד שיעשה גם עיבוד גס (מקדים) וגם עיבוד סופי.
בתוכנת "סימטרון" קיימת אופציה לבצע את החלק בשלבים שונים עם כליי עיבוד אחרים תוך התחשבות בחומר שהשאיר כלי אחד למשנהו. לדוגמא: עם הכלי הראשון (מרסק 20 מ"מ) מבצעים את כל עבודת הסרת החומר הראשונית, עיבוד גס במדרגות גדולות עם היסט של 0.2 מ"מ מהמידה הסופית. הכלי הזה כמובן אינו יכול להגיע לכל פינות החלק ומשאיר מדרגות גסות לכן ניקח כלי שני (מרסק 10 מ"מ) ונמשיך את פעולת הסרת החומר הגס במדרגות קטנות עם אותו היסט (0.2 מ"מ מהמידה הסופית).
מאחר ותוכנת ה"סימטרון" יודעת בכל שלב של העבודה את כמות החומר שהוסרה ואת כמות חומר גלם שיש להסיר, היא תייצר מהלכי עבודה לכלי השני אך ורק באזורים בהם נישאר חומר גלם להסיר, כך שלא יוצרו מהלכים מיותרים באוויר. כתוצאה מעיבוד מקדים זה לכלי הגמר נישאר היסט אחיד מסביב של 0.2 מ"מ מהמידה הסופית כך המאמצים שיהיו עליו יהיו אחידים ואורך חיי הכלי יהיה ארוך יותר.
גם את העיבוד הסופי למידה, התוכנה מאפשרת לעבד בכמה כלים (בדר"כ כדוריים, או שטוחים עם רדיוס פינה) בטכנולוגיה זהה, כך שהמפעיל בוחר את רצף הכלים בה הוא רוצה להשתמש (מהגדול לקטן) ותוכנת ה"סימטרון" מחשבת בצורה אופטימאלית את מהליכי הכלי תוך
התחשבות מרבית בכמות חומר הגלם שהשאיר הכלי הקודם והיכולת של הכלי הנוכחי להסיר את החומר שנישאר.
יכולת חזקה זו של תוכנת "סימטרון" מאפשרת למפעיל גמישות מקסימאלית ביצור החלק או בשינויים "הנופלים" עליו בזמן התכנות. לדוגמא: החלק שונה ע"י המתכנן, אין כלי מתאים במפעל, הצורך לעשות חלקים דומים אך במידות שונות וכו'.
עד כה סקרתי כמה מהתפתחויות האחרונות בתחום התיב"מ המכאני, אך האם הגענו לקצה גבול יכולת הפיתוח בתחום זה? לדאבוני אין אני יכול לענות על שאלה זו, מאחר והשינויים בענף הכלים ומכונות העיבוד שבבי הם מהפכניים מתקופה לתקופה.
לסיכום אציג את הדור הבא בתיב"מ המכאני כפי שאני צופה לעתיד:
לאחר תיכנון ועיצוב המוצר מועבר מודל מתמטי (solid) למחלקת היצור. תוכנת התיב"מ "הדור הבא" פורסת את המודל לפרוסות אופקיות בעובי של מיקרון המילימטר לשיכבה, על פי חיתוך שכבות אלו בונה "מדפסת העל" את החלק מלמטה למעלה שכבה על גבי שיכבה. (בדומה לשיטת ה- Stereo Lithography, בניית מודל תלת ממדי מחומר פולימרי כלשהוא).
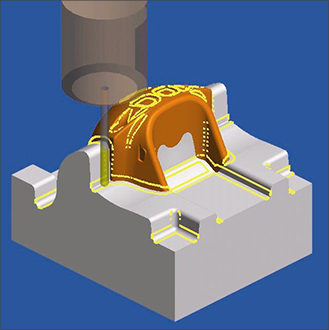
בטכנולוגיה חדשה זו נוכל ליצר כל חלק בכל צורה אפילו אם לא ניתן היה ליצרו בעיבוד שבבי בטכנולוגיה הידועה כיום, ולהלן כמה מהיתרונות מ"הדפסה" זו:
המעבר ממודל לתחילת יצור יהיה עניין של דקות, החלקים ייצורו מכל חומר נידרש כולל סוגי מתכות שונות קשות ו/או בלתי ניתנות לעיבוד שבבי, מהירות היצור תהייה כמהירות הזרקת פלסטיק בתבנית (שניות בודדות למנה), כמות חלקים רבה תיוצר במנה אחת, טיב פני שטח מעולה N1-N3, תכונות החומר לא ישתנו או נקבל טובות יותר (קשיות, חוזק, כיוון סיבים וכו'), ציפוי חיצוני רצוי ומעל לכל הדיוק של כל החלקים יהיה כנדרש וזהה בכולם.
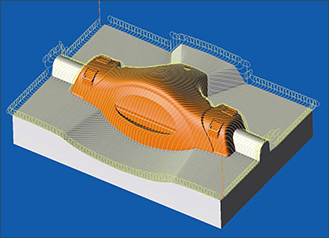
ובכן, האם תיב"מ "הדור הבא" הוא דמיוני? חכו עשור אחד או שניים ותראו את החזון מתגשם.
למידע על עיבוד שבבי כנסו ללינק